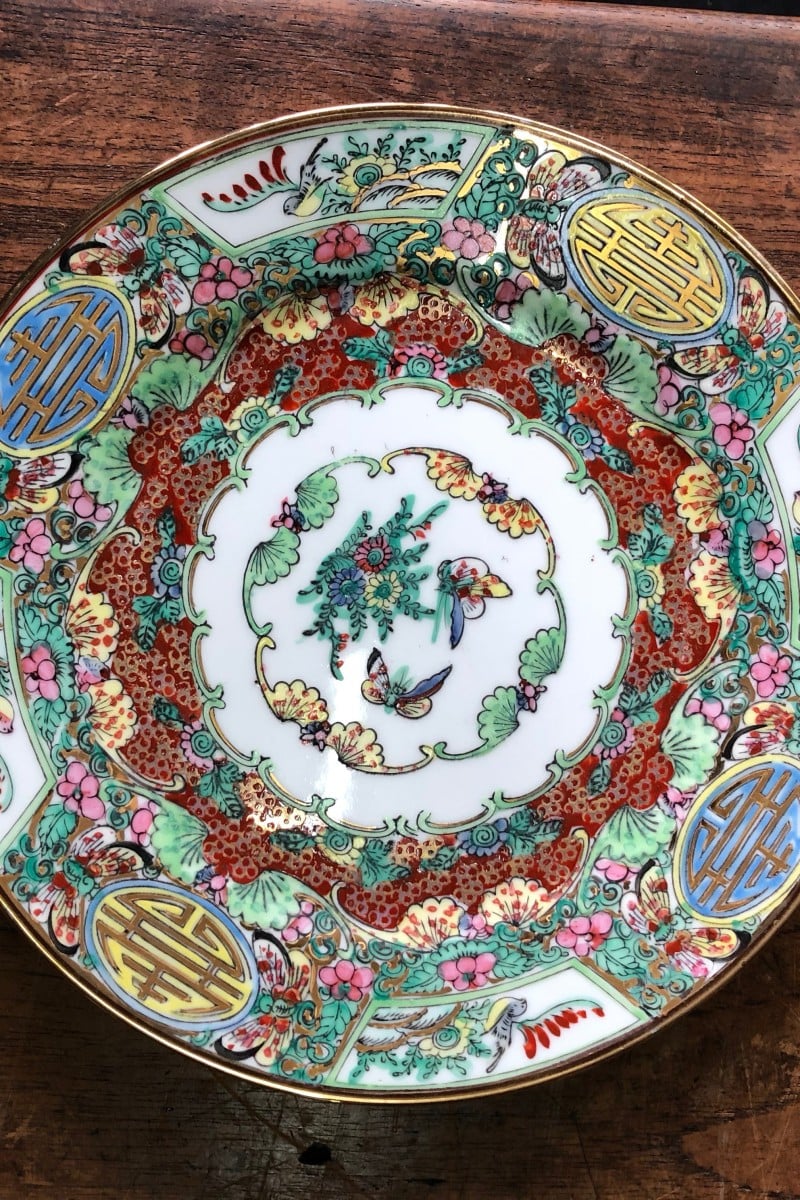
What sets Hong Kong Cantonese porcelain apart from the rest, and why it's a tradition worth preserving
Joseph Tso Chi-chung, one of Hong Kong’s top hand-painted porcelain craftsmen is determined to safeguard the art form
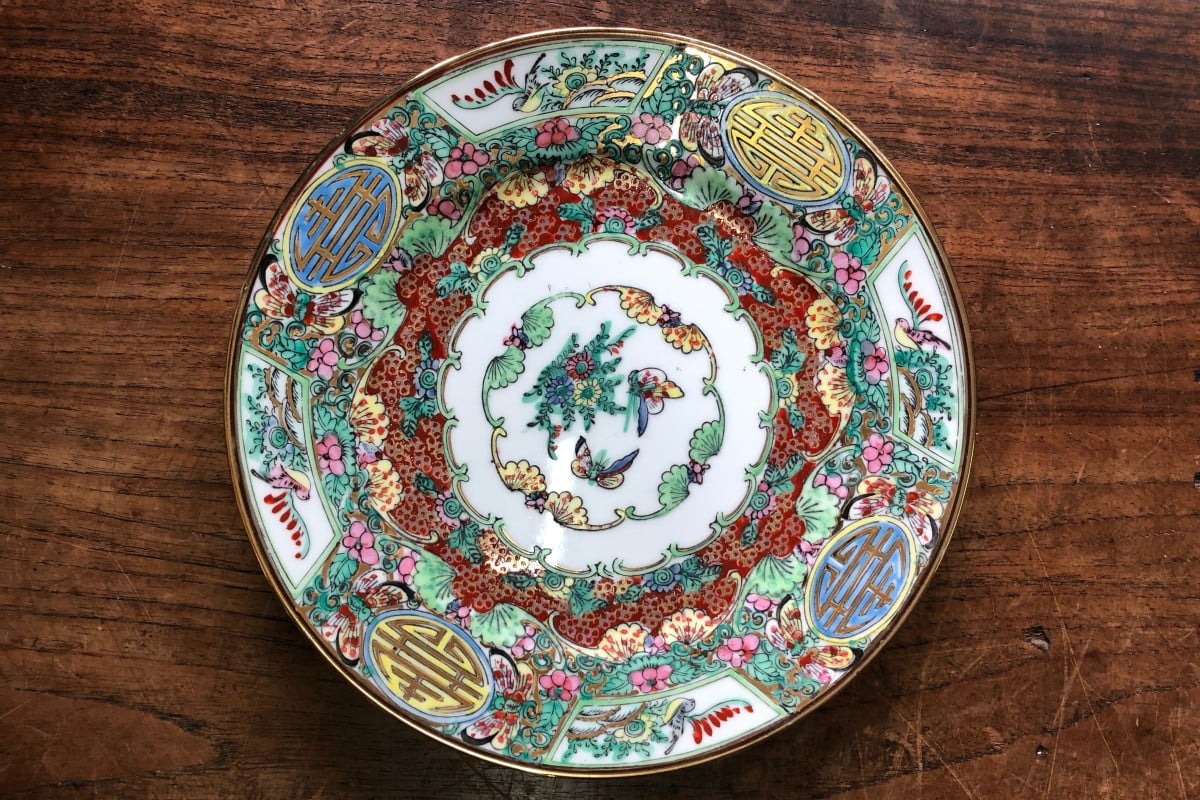
Hand-painted Cantonese porcelain, known as guang cai, or choi chi in Cantonese, was once considered one of the economic pillars of Hong Kong, with more than 1,000 craftsmen working in the city. Since its heyday in the mid-20th century, however, the industry has been rapidly declining. Young Post met Joseph Tso Chi-chung, one of the few remaining Cantonese porcelain artisans left in Hong Kong.
Tso still runs his own business in Kowloon Bay, Yuet Tung China Works – the first hand-painted porcelain factory in Hong Kong. Established in 1928 by Tso’s grandfather, Yuet Tung still has a reputation for producing high-quality porcelain goods.
Tso started working at the factory in 1956 and took over the company in 1968.
“I was asked to help out at Yuet Tung because I was quite good at English, and was able to communicate with foreign buyers,” Tso recalled. “Then I became interested in porcelain making and stayed on. But it wasn’t until, I was a student at Hong Kong Baptist College that I started taking up a larger role in the factory.”
When asked what makes the craft so unique, Tso said that “Cantonese porcelain, like Hong Kong culture, is a mix-and-match of Western and Chinese culture, retaining the best of both worlds."
Producing Cantonese porcelain requires patience and effort. First, plain white porcelain of the highest quality is selected and bought from mainland factories. A painter can then use one of two decorating methods: transfer-printing or stamping.
In transfer-printing, the pattern is first sketched, then produced in the form of a full-colour sticker. The sticker is placed on the porcelain, which is then baked in a kiln to make the design permanent.
The stamping method involves printing the initial pattern onto a rubber sheet to make a stamp. The stamp is then coated with black glaze and pressed on the porcelain to transfer the pattern. Colours are added afterwards. Finally, the porcelain is baked in a kiln.
The traditional family business of crafting a Tuen Ng festival dragon boat
As well as pioneering these methods in Hong Kong, Tso is also credited as being one of the forerunners of producing customised porcelain goods for both local and foreign buyers.
Tso believes that innovation is the key to success. “In the past, foreign buyers would request family crests or other special objects to be added to the patterns on the porcelain. Nowadays, to combat rising production costs and compete with cheaper goods produced on the mainland, we have introduced an even higher degree of customisation.”
Tso firmly believes that porcelain making is a tradition that is worth protecting, and that it is his duty to help keep it alive. “I am one of the few remaining Cantonese porcelain artisans in Hong Kong.
I feel like I’m responsible for helping to preserve this tradition so that future generations are still able to appreciate and learn about porcelain making on a first-hand basis.”
Tso’s dedication to his craft has led him to collaborate with local schools. “I have been working with various schools all over Hong Kong to host workshops for secondary school students who are interested in porcelain making. I hope my efforts will help to preserve this art form.”
Tso also holds other workshops for teenagers in his factory for free. “I’m just contributing the little that I can. I just really hope that this can help to draw more attention to Cantonese porcelain making.”