Kiton’s bespoke suits are haute couture for men: STYLE visited the Italian fashion house to see the making of a US$100,000 K50 suit – video
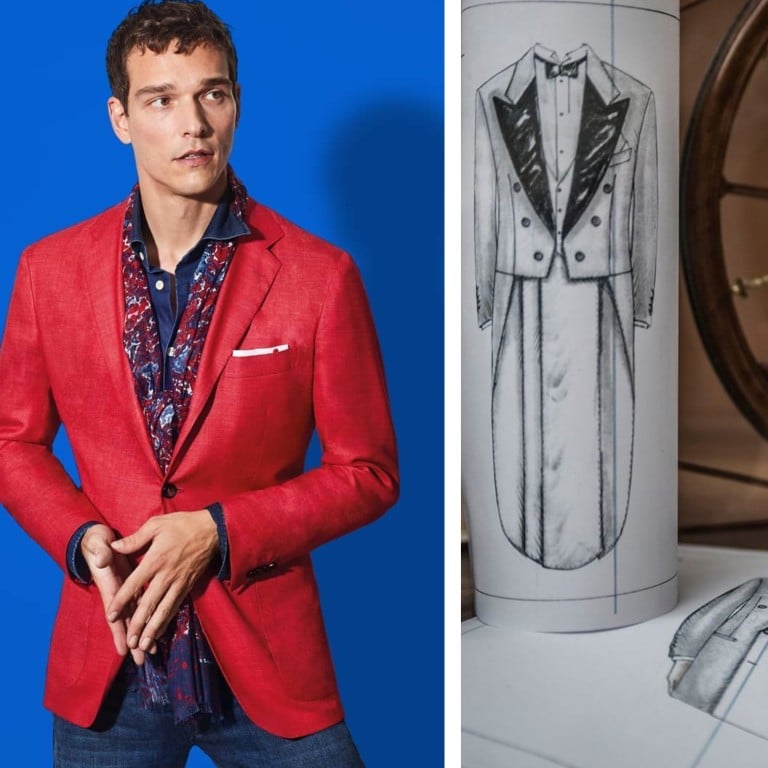
Founded by textile visionary Ciro Paone, Kiton is a bastion of Campania’s artisanal tailoring skills, using baby cashmere and 12.8 micron wool, and 25 to 50 hours of handicrafting, to create its suits
Tucked away behind a palm tree-lined avenue on the outskirts of Naples is the Kiton workshop – a mythical place where rolls of ultrafine fabric arrive at one end of the building and some of the world’s most expensive suits leave at the other.
We received a rare invitation to look behind the scenes at this Italian temple of tailoring.
Stepping into Kiton’s elegant HQ, where the workers set down their shears at lunchtime to enjoy leisurely, home-cooked meals washed down with red wine, it quickly becomes clear that this is no ordinary clothing factory. Instead, this is a workplace of quiet dignity where the time-honoured skill of creating by hand is alive and kicking.
Founded in 1968 by visionary textile aficionado Ciro Paone, Kiton remains a family-run business, albeit one that now boasts 54 single-brand boutiques globally. Their on-site tailoring school ensures that the bespoke baton is passed down to future generations. Following a three-year training, many of these apprentice tailors will graduate onto the Kiton workshop floor.
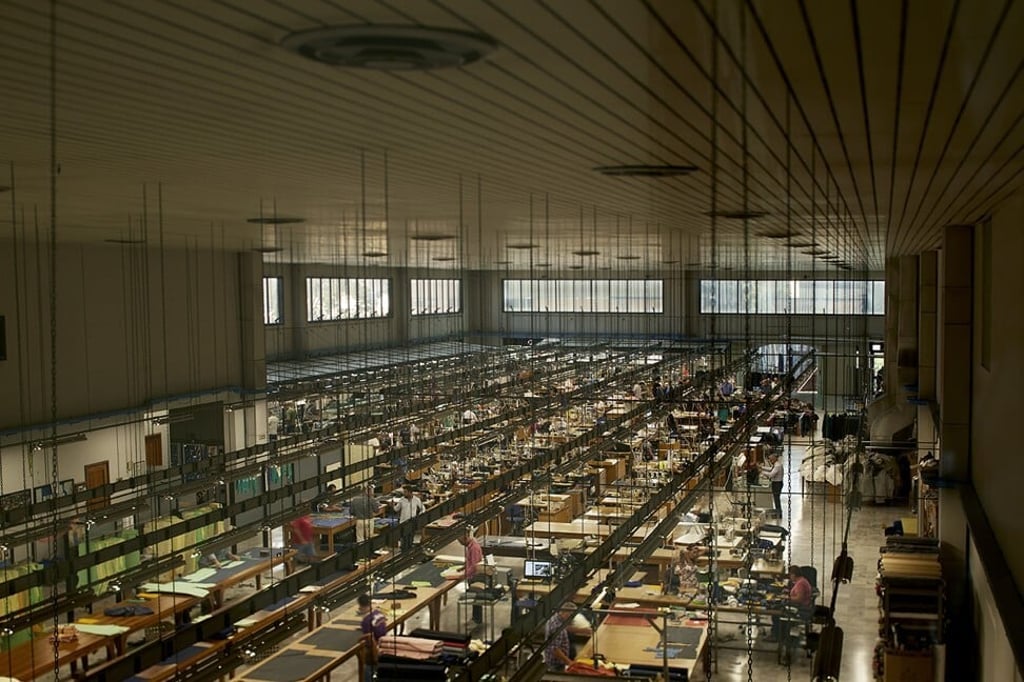
It’s here that the real action takes place, as suits make their journey through each specialised stage of production. On average, a Kiton suit requires an impressive 25 hours of labour, with the bulk of the work being stitched by hand. Using superfine materials such as baby cashmere and 12.8 micron wool, the finest thread in the world which is notoriously difficult to work with, workers lay the fabrics out on vast wooden tables and chalk the shape of the blocks onto the surface. A key element of the Kiton suit is its symmetry, which is particularly visible when check or pinstripe textiles are used.
Once the jacket has been cut and the exterior assembled, a silk lining is then stitched in with a layer of canvas sandwiched between the silk and the suit fabric, creating a floating canvas. Finally, the finishing touches are applied before it is given a concluding inspection by the unforgiving master tailor and placed on the rail, ready for dispatch to the customer.
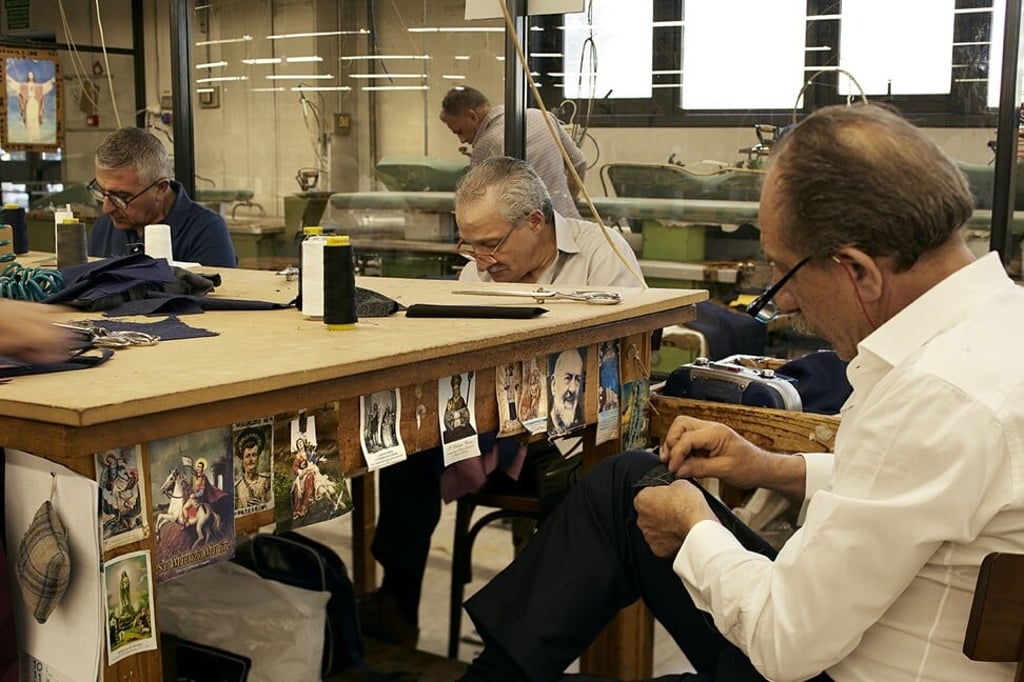
Kiton has long been recognised as one of the sartorial greats – an ultra-luxe brand upholding the artisanal skills of the local Campania region. The pinnacle of this ethos has to be their K50 suit, delicately created from start to finish by a single master tailor. These suits require 50 hours of intricate hand stitching and there are only 10 tailors in the Kiton workshop qualified to take on this level of craftsmanship.